Custom Kiln Drying
Live Edge
All wood thank includes live and uneven edges.
- Wood type live edge
- Thickness 6 / 4 and under
- Thickness 8 / 4 and over
Lumber
Straight edge and ready to use
- Wood type Lumber
- Thickness 4 /4 - Less than 10 days
- Length Up to 13' long
We use an iDRY Vacuum kiln. All iDRY models promise the same fast, reliable and efficient drying , using a combination of heat and vacuum, iDRY Turbo dries lumber and squares from 4/4 to 16/4 ten times faster than conventional kilns, while the iDRY and iDRY PLUS dry about 5 times faster.
Running a dedicated sterilization cycle is not usually done by dehumidification kilns.
Because wood has been kiln dried does not mean it is sterilized, as most DH kiln cycles top out at 120 degrees, not high enough to properly sterilize. It takes special effort, time and expense to do so. If you purchase wood from other sources, ask them if they perform a dedicated sterilization step. Most likely they will give you a “What?” look.
Air dried wood is not sterilized, no matter how long it has been drying, and since the incubation period for certain insects can take years, not seeing bugs when you buy air dried wood doesn’t mean they aren’t in there. As an interesting observation, I have never kiln dried and sterilized live edge slabs where there weren’t dead bugs on the wood when the cycle was finished. Never. Live edge slabs will always have bugs under the bark or in the cambium layer. The only way to kill them is with heat, and we sterilize every single load of wood that comes out of our kilns.
All iDRY kilns use a vacuum to create a pressure gradient between the shell and the core of the wood. Conventional drying methods rely on moisture differential or gradient to move the water from the wetter core toward the dryer shell. This can be a slow process since the operator must be careful not to over dry the shell or degrade will result. The iDRY achieves its fast drying rates by maintaining a small differential between the shell and the core moisture contents throughout the drying period. Typically, the core of the wood is essentially at atmospheric pressure, while the shell of the wood is at a much reduced pressure, causing the water to flow toward the shell more rapidly.
When drying lumber it is necessary to increase the temperature while maintaining a vacuum. This causes the environment within the dryer to become superheated and therefore the equilibrium moisture content is reduced causing the moisture from the wood to convert to water vapor at the reduced pressure. The moisture from the wood can then be condensed and removed from the pressure vessel and drained via the floor drain or vacuum pump.
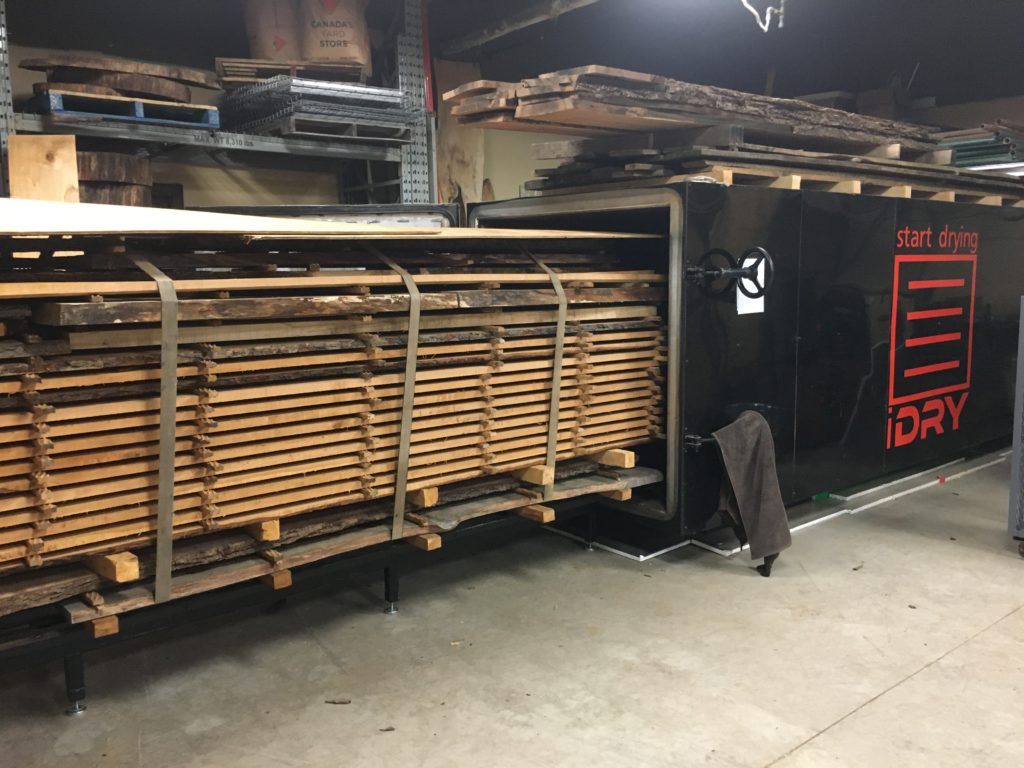
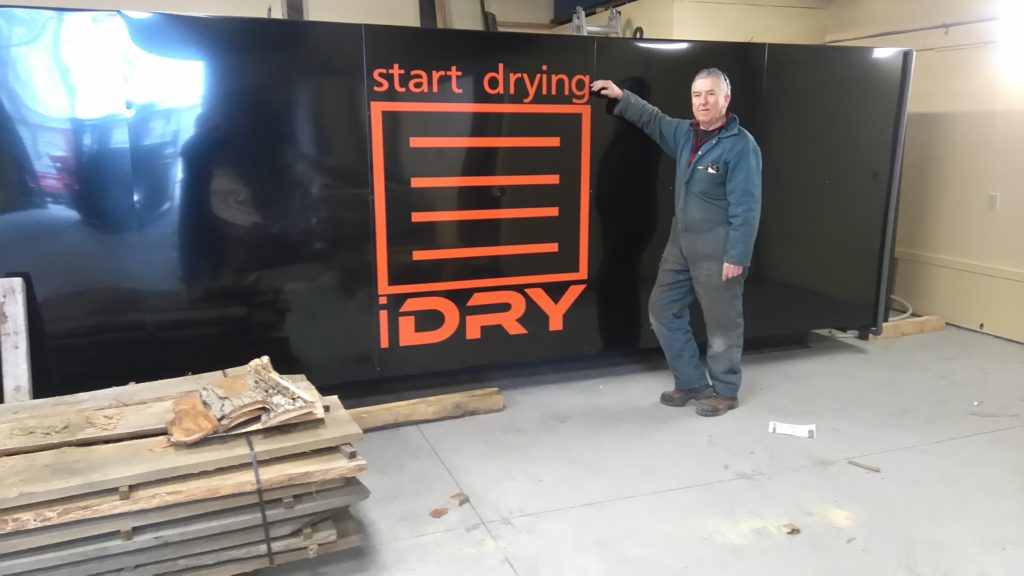
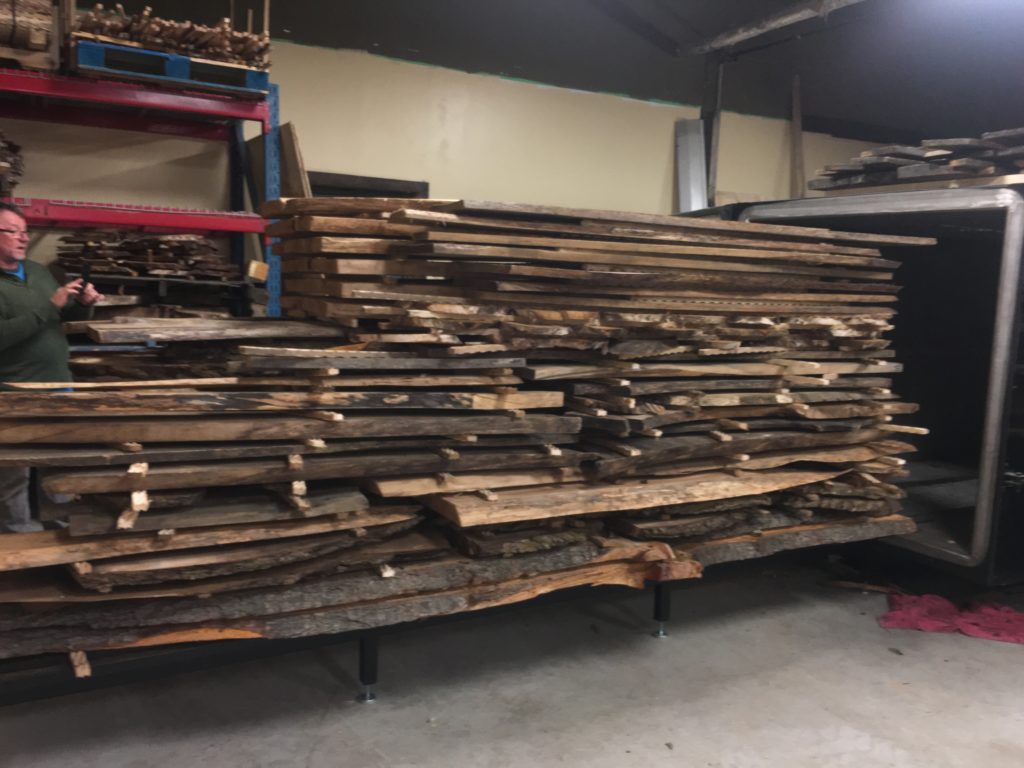